Micro Robots an Overview and Topics
Micro Robots is a robotics kit sold by Thames and Kosmos. The kit is designed to allow the user to build a variety of small robots from a kit that contains over 550 parts. The robot can then be controlled using a computer, phone, or tablet.
In this article, we will take a look at the kit and some of the possible projects that can be made.
Introduction to Micro Robots
Micro robots are tiny robots that can be controlled using a computer. They are used in a variety of applications, including research, manufacturing, and military applications.
In this article, we will overview the different types of micro scale robots, and discuss some of their most popular applications.
What are Micro Robots?
Micro Robots are tiny machines that are used in a variety of applications. They are often used in research, manufacturing, and surveillance.
In this article, we will discuss some of the most common topics related to micro robots.
Topics Covered:
1. What are the different types of micro robots?
2. How are micro robots used in research?
3. How are tiny robots used in manufacturing?
4. How are micro robots used in surveillance?
5. What are the benefits of using micro robots?
6. What are the challenges of using micro robots?
7. How can the use of small robots be improved?
8. What are the future trends of micro robots?
9. What are some applications of micro robots that are still under development?
10. What are the ethical considerations of using micro robots?
11. What are the future prospects for microrobots?
What are the Components of Micro Robots?
Microrobots are small, often programmable robots that can be controlled with a computer. They are often used for tasks such as inspection and inspection planning, manufacturing, and research.
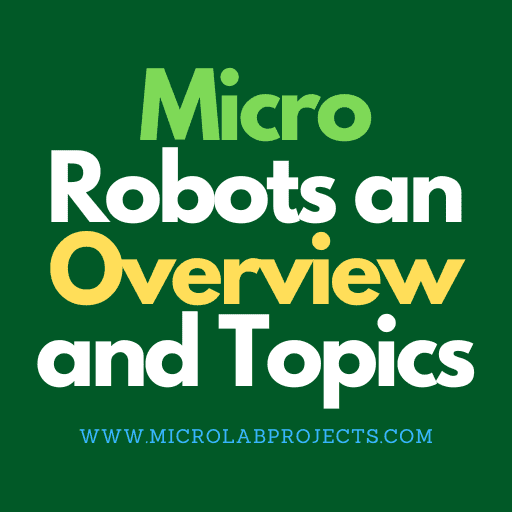
There are many different types of micro robots, each with its own specific set of features. In this article, we will discuss the different components of micro robots, as well as some of the common tasks that they are used for.
Related Articles
- Introduction to Micro Robots
- Design Considerations for MicroRobots
- Control of Micro Robots
- Micro Robot Mobility
- Conclusion
Micro robots are made up of three main components: the robot body, the controller, and the sensors. The robot body is the physical part of the robot that you can see and touch. It contains the motors, sensors, and other electronics that allow it to be controlled.
The controller is the central part of the microrobot system. It is responsible for controlling the robot’s movements and settings, and communicating with the sensors and other components.
The sensors are the main sensors on a micro robot. They are used to detect information such as the robot’s position, motion, and temperature.
What are the Types of Micro Robots?
There are a few different types of micro robots, each with its own unique set of features and capabilities.
Here are the different types of micro robots:
1. Micro robots that are powered by electricity: These robots are the smallest and simplest of the bunch, and are the most common type of robot. They are powered by electricity, and can be controlled using a variety of different devices.
2. Micro robots that are powered by batteries: These robots are a bit larger than the electric powered robots, and are capable of longer distances. They are also more versatile, as they can be used for a variety of different tasks.
3. Micro robots that are powered by fuel: These robots are the largest and most complex of the bunch. They are also the most expensive, and are used for the most complex tasks.
4. Micro robots that are powered by both electricity and fuel: These robots are a combination of the two different types of robots, and are the most versatile of the bunch. They are able to do a variety of tasks, and are the best choice for those who want to have a multifunctional robot.
What are the Applications of Micro Robots?
Micro robots are being explored for a variety of applications due to their small size and flexibility. Here are a few examples:
1. Factory automation: Micro robots can be used in factories to help with tasks such as moving parts, cleaning, and assembling.
2. Medical applications: Micro robots can be used in medical procedures to help with tasks such as surgery, wound healing, and monitoring.
3. Retail: Microrobots can be used in retail settings to help with tasks such as inventory management, customer service, and stocking shelves.
4. Agriculture: Micro robots can be used in agriculture to help with tasks such as harvesting, weeding, and monitoring crops.
5. The military: Microrobots can be used in the military to help with tasks such as reconnaissance, target identification, and bomb disposal.
6. Home appliances: Microrobots can be used in home appliances to help with tasks such as cleaning, assembling, and repairing.
7. Manufacturing: Microrobots can be used in manufacturing to help with tasks such as welding, assembly, and quality control.
8. Entertainment: Micro robots can be used in entertainment to help with tasks such as filming, directing, and staging.
9. Research: Microrobots can be used in research to help with tasks such as exploring new environments, gathering data, and performing research experiments.
Design Considerations for Micro Robots
As we move towards more and more miniature robots, it is important to keep in mind the design considerations that go into making them. In this article, we will explore some of the key considerations for micro robots, and how to make sure that your designs are successful.
First and foremost, it is important to consider the size and weight of the robot. Tiny robots need to be able to maneuver easily and be light enough to be moved around. They also need to be able to communicate with one another and be able to sense their environment.
Another important consideration is the power and communication capabilities of the robot. Micro robots need to be able to send and receive information rapidly, as well as be able to interact with their surroundings. They also need to be able to operate in a range of environments, from small and confined spaces to large open spaces.
It is important to be creative when designing micro robots, and to think of ways to make them unique and interesting. By following these design considerations, you can make sure that your microrobots are successful and meet the needs of your users.
What are the Design Considerations for Micro Robots?
When designing for micro robots, there are a few things to keep in mind.
First, the size and shape of the robot must be considered. The smaller the robot, the fewer parts it has, and the more complex the design.
Second, the materials used must be lightweight and easy to move. This is important because the smaller and lighter the robot, the less energy it requires to move.
Third, the design must be able to withstand a variety of environments. This can include different types of weather, vibrations, and collisions.
Fourth, the design must be easy to operate. This includes making sure the controls are easy to use and the robot can be assembled and disassembled in a matter of minutes.
All of these considerations must be taken into account when designing a micro robot. If done correctly, it can result in a sleek, efficient design that can be used in a variety of applications.
What are the Challenges in Designing Micro Robots?
There are many challenges in designing micro robots.
One of the biggest challenges is the miniaturization of the robots. They have to be small enough to fit inside small spaces, but also robust enough to handle difficult tasks.
Another challenge is the ability to control the robots remotely. They need to be able to move around, interact with their surroundings, and carry out tasks without getting stuck.
Lastly, the robots need to be able to communicate with each other, so that they can work together as a team.
What are the Materials Used for Micro Robots?
Micro robots are made of different materials, depending on what they are designed to do. Some common materials used for micro robots include plastics, metal, and even silicone.
There are pros and cons to each material, so it is important to choose the right one for your robot. Plastic microrobots are lightweight and easy to move, but they can be brittle and susceptible to damage.
Metal micro robots are strong and can handle a lot of punishment, but they can be heavy and expensive. Silicone microrobots are popular because they are flexible and can withstand a lot of abuse, but they can be difficult to manufacture.
It is important to choose the right material for your micro robot, because it will affect the performance and lifespan of the robot.
What are the Basic Design Principles for Micro Robots?
Micro Robots are designed to have a very small size, making them perfect for specific tasks. This miniaturization allows for a number of design principles to be applied that would not be possible with larger robots.
One of the most important principles is that microrobots must be able to move in all directions. This is important for tasks such as navigation and inspection, as well as for moving parts around.
Another important principle is that micro robots must be able to sense their environment. This is done through sensors and actuators, which allow the robot to respond to obstacles and changes in its surroundings.
Control of Micro Robots
Controlling micro robots is essential for a variety of tasks, from manufacturing to research. In this article, we’ll be looking at the basics of controlling microrobots, as well as some common tasks that they’re used for.
Micro robots are often used in manufacturing to replace humanworkers. By automating certain tasks, micro robots can help speed up the manufacturing process. They’re also used in research labs, where they can be used to probe inside objects.
By understanding the basics of controlling micro robots, you’ll be able to use them for the tasks that they’re best suited for.
How are Micro Robots Controlled?
Micro robots are controlled by a controller that sends a signal to the robot that tells it what to do. The controller can be in the form of a computer, a microcontroller, or a sensor. The controller can also be in the form of a human.
There are many types of controllers, but all of them work the same way. The controller sends a signal to the robot, and the robot follows the signal.
There are many different ways to control a micro robot. The most common way is to use a controller. A controller is a device that sends a signal to the robot. The controller can be in the form of a computer, a microcontroller, or a sensor. The controller can also be in the form of a human.
There are many different ways to control a micro robot.
What are the Different Control Strategies for Micro Robots?
There are a few different control strategies that you can use with micro robots.
The first strategy is to use a remote control. This allows you to control the robot from a distance.
The second strategy is to use a wireless controller. This allows you to control the robot without having to be in close proximity.
The third strategy is to use a headless controller. This allows you to control the robot without having a specific destination in mind.
The fourth strategy is to use a GPS controller. This allows you to track the location of the robot.
The fifth strategy is to use a camera. This allows you to capture images and videos of the robot.
What are the Control Algorithms for Micro Robots?
There are many different control algorithms for micro robots. In this article, we will discuss the three most common algorithms, PID, proportional-integral-derivative (PID), and fuzzy logic controller (FLC). We will also discuss their advantages and disadvantages.
PID is a two-state control algorithm that uses a state variable to determine the control action. The state variable is a proportional input to a controller. The controller uses the state variable to make a decision about the control action. PID is simple to implement and is the most common control algorithm for micro robots.
PID has the advantage of being simple to implement and is used in many industrial robots. It has the disadvantage of being susceptible to over-steer and under-steer.
PID is also the most commonly used control algorithm for microrobots in research projects.
PID has the disadvantage of being susceptible to over-steer and under-steer.
PID is the most common control algorithm for microrobots in research projects.
PID has the advantage of being simple to implement and is used in many industrial robots. It has the disadvantage of being susceptible to over-steer and under-steer.
PID is also the most commonly used control algorithm for micro robots in research projects.
What are the Different Types of Sensors Used for Micro Robots?
There are a variety of different sensors that are commonly used in micro robots. These sensors can be used for a variety of purposes, such as detecting obstacles, mapping terrain, and measuring distances.
Here are the different types of sensors that are commonly used in micro robots:
1. accelerometers: These sensors are used to detect changes in movement, such as when an object is moving or when the micro robot is moving.
2. gyroscopes: These sensors are used to keep track of the orientation of the micro robot.
3. magnetometers: These sensors are used to detect changes in the magnetic field.
4. GPS receivers: These sensors are used to track the location of the micro robot.
5. barometers: These sensors are used to measure the pressure in the air.
6. touch sensors: These sensors are used to detect the presence of humans or other objects.
7. ultrasonic sensors: These sensors are used to detect objects that are smaller than the wavelength of the ultrasound.
8. cameras: These sensors are used to capture images or videos.
9. ultrasonic emitters: These sensors are used to produce ultrasound waves.
10. light sensors: These sensors are used to detect light.
11. pressure sensors: These sensors are used to detect changes in pressure.
12. temperature sensors: These sensors are used to detect changes in temperature.
Micro Robot Mobility
Micro robots are miniature robots that have been shrunken down to the size of a microchip. They are used in a variety of applications such as industrial inspection, security and surveillance, and manufacturing.
In this article, we will be discussing microrobots in general and some of their most popular applications. We will also cover some of the topics that are related to their mobility such as locomotion, sensors, and control systems.
Micro Robots are miniature robots that have been shrunken down to the size of a microchip. They are used in a variety of applications such as industrial inspection, security and surveillance, and manufacturing.
In general, micro robots are used for tasks that are too dangerous, tedious, or time-consuming for humans to complete. They are also used in situations where there is a high demand for precision or where the size or weight of the robot is a limitation.
Some of the most popular applications of micro robots include industrial inspection, security and surveillance, and manufacturing.
In industrial inspection, microrobots are used to inspect delicate parts or areas that are too dangerous for humans to reach. They are also used in situations where the size or weight of the robot is a limitation.
Security and surveillance applications are another popular use for microrobots. They are used to monitor areas that are too difficult or dangerous for humans to reach.
Manufacturing is another area where micro robots are used extensively. They are used to monitor and control the production process.
What are the Different Mobility Strategies for Micro Robots?
Micro robots are becoming more popular as they offer an increased level of versatility and efficiency. In this article, we will discuss the different mobility strategies that are available for microrobots.
There are three mobility strategies that are used for micro robots: encased, unencased, and jointed. Encased microrobots are those in which the robot is completely enclosed by a shell or housing.
Unencased micro robots have a limited amount of housing that does not enclose the robot completely, and jointed microrobots are those in which the robot has movable joints that allow it to move in different directions.
Each mobility strategy has its own advantages and disadvantages. Encased micro robots are the most versatile, as they can be used in a variety of environments and can be easily transported. However, they are also the most expensive and difficult to build.
Unencased micro robots are cheaper and easier to build, but they are limited in terms of their environment and mobility. Jointed micro robots offer the best of both worlds; they are able to move in a variety of directions, but are also relatively easy to build and are less expensive than encased micro robots.
What are the Different Locomotion Techniques for Micro Robots?
There are a few different locomotion techniques that can be used for micro robots.
Rotating: This is the most common locomotion technique for micro robots. They will usually rotate on their axes to move around.
Swimming: Micro robots that swim are able to move through water by using their propellers to move forward.
Flying: Micro robots that fly use lift to move through the air.
What are the Different Actuation Mechanisms for Micro Robots?
There are a few different Actuation Mechanisms that we use for micro robots. These mechanisms can be classified into two groups: actively driven and passive.
Active driven mechanisms use a motor to power the robot and allow it to move. Passive mechanisms do not use a motor, and instead rely on a spring or a weight to keep the robot in place.
The different Actuation Mechanisms have different advantages and disadvantages.
For example, actively driven mechanisms are more powerful, but they can also be more difficult to control. Passively driven mechanisms are easier to control, but they are less powerful.
In this article, we will discuss the different Actuation Mechanisms and their advantages and disadvantages.
What are the Different Power Sources for Micro Robots?
Micro robots are powered by a variety of different power sources. These power sources can include batteries, solar panels, and motors. In this article, we will discuss each of these power sources in detail.
Batteries: Micro robots can be powered by batteries. These batteries are small and can be easily carried around. They are also affordable, making them a popular choice for micro robots.
Solar Panels: Microrobots can also be powered by solar panels. These panels are large and can be mounted on the robot. They are also expensive, but they offer a long lasting power source for the robot.
Motors: Microrobots can be powered by motors. These motors can be small or large, and they can be used to move the robot around. They are also affordable, making them a popular choice for micro robots.
Finally
In this blog post, we will be discussing micro robots and their potential applications. We will also be covering some of the topics that are related to microrobots. We would love to hear your thoughts and feedback on this post.
Micro robots are fascinating devices that can be used for a variety of purposes. Their potential applications are vast and continue to grow as research and development progress. We hope you have enjoyed this blog post and we look forward to hearing your thoughts and feedback.
What are the Potential Applications of Micro Robots?
Micro robots are fascinating devices that can be used in a variety of different ways. Some potential applications of microrobots include surgery, manufacturing, and research. In this article, we will explore the different types of microrobots and their potential applications.
Types of Micro Robots
There are two main types of micro robots: crawling and flying. Crawling microrobots are tiny robots that move on all fours.
They are often used in surgery because they are able to navigate tight spaces and maneuver around obstacles.
Flying micro robots are similar to traditional airplanes, except they are much smaller. They are often used in manufacturing because they are able to move quickly and reach high altitudes.
Other Potential Applications
Microrobots have a lot of potential applications that we haven’t even mentioned yet. They could be used in research to study different aspects of the world.
They could also be used in the manufacturing industry to help automate processes. There are endless possibilities for micro robots, and the applications only continue to grow.
What are the Future Directions for Micro Robots?
Micro robotics is quickly becoming a popular technology due to its potential in a variety of fields. Micro robots can be used for a wide variety of purposes, including manufacturing, research, and healthcare. In this overview, we will discuss the future directions for micro robots and the various applications for which they are being used.
One of the most popular uses for micro robotics is manufacturing. Micro robots can be used to create products faster and more accurately than traditional methods. They are also able to work in difficult and dangerous environments, which is an advantage over traditional manufacturing methods.
Micro robotics has also been used in research. Micro robots are able to move and interact in ways that are difficult or impossible for larger robots. This is used in a wide variety of fields, including medicine, agriculture, and manufacturing.
Micro robots are also being used in healthcare. Micro robots are able to navigate hospitals and clinics much more easily than human beings. They are also able to interact with patients in ways that are more comfortable for them. This is an important step in making healthcare more comfortable for patients.
What are the Challenges for Micro Robots?
There are a few fundamental challenges that need to be addressed when working with micro robots.
Conclusion
Conclusion Micro Robots are being used in many industries for a variety of purposes. In this blog post, we will be discussing some of the advantages and disadvantages of using micro robots.
Advantages of using micro robots include their small size, which allows them to enter tight spaces and their ability to move quickly. Disadvantages of using micro robots include their high cost and the fact that they are not always effective.
We will also be discussing some of the topics that are covered by micro robots. These topics include 3D printing, fabricating and welding. stay tuned for more!
FAQs About Micro Robot
What is a micro robot?
A micro robot is a small robot that typically has a width of less than two inches and a length of less than four inches. They are often used for research, manufacturing, and inspection.
What are the different types of micro robots?
There are various types of micro robots, including swarm robots, medical robots, micro aerial vehicles, and microelectromechanical systems (MEMS) robots.
What are some applications of micro robots?
Micro robots have a wide range of applications, including medical procedures, environmental monitoring, search and rescue operations, and industrial manufacturing.
How are micro robots powered?
Micro robots can be powered by batteries, solar cells, or other energy sources, depending on their specific design and application.
What are the challenges of designing and building micro robots?
Designing and building micro robots can be challenging due to their small size and the need to pack in all the necessary components and functionality. Power management, control, and communication can also be difficult in such a small form factor.
How can micro robots be controlled?
Micro robots can be controlled through various means, including wired or wireless communication, onboard sensors, and autonomous decision-making algorithms.
What is the future of micro robots?
The field of micro robotics is rapidly advancing, with new developments in materials, sensors, and control systems enabling increasingly complex and capable micro robots. It is expected that micro robots will continue to play an important role in a wide range of industries and applications in the future.
We designed a rolling micro robots the size of an insect driven by continuously rotating wheels. It measures 58 mm and 24 mm There are 2 versions of the robot: one of 96 mg with laser and one of 130 mg with supercapacitor.
The robot can move at 127 mm / s (1.5 body lengths per second) with wheels that rotate at 300 ∘/ s, while consuming an average power of 2.5mW.
None of the versions have electrical cables, and the supercapacitor robot is also self-sufficient and can roll freely for 8 seconds after a single charge.
Micro Robots – an Overview and Topics
Low voltage electromagnetic actuators (1V-3V) together with a new double ratchet mechanism allow the operation of this device. It is, to the best of our knowledge, the lightest and fastest self-sufficient rolling micro-robot reported so far.
Soft microrobots represent end effectors of electromagnetic and permanent magnet-based manipulation systems. These microrobots can navigate under the influence of a controlled magnetic field.
We are interested in the precise control of the micro robots like remote control helicopter. Therefore, the field of action should be designed to simultaneously propel and steer the micro robots along a prescribed trajectory.
The magnetization of the 1 cubic inch micro robot and the relationship between the control inputs and the field of the manipulation system are important factors in the design of a control system.
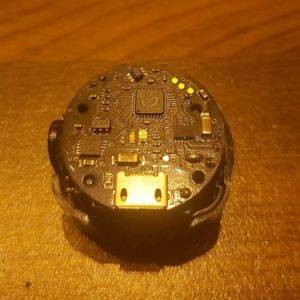
This chapter begins with an introductory modeling of the magnetic torque on soft magnetic materials and actuation systems. We then demonstrate an open-loop control framework for a variety of soft microrobots to move them along a prescribed trajectory.
Soft Microrobots
Micro robot could also be used for minimally invasive surgery. Examples of surgical procedures that could be performed by a micro robots include opening blocked vessels or other ducts, cauterization, treatment of hyperthermia, biopsies, electrical stimulation, injection, cutting, drilling, or biomaterial removal.
To date, several groups have investigated the use of integrated capsule endoscope biopsy tools to collect tissue samples for diagnostic purposes.
Extending these capabilities to surgical micro robots would allow for more precise targeting of sampling sites using a minimally invasive surgical system. Others have proposed magnetic robots that could be used to puncture or open blockages in blood vessels.
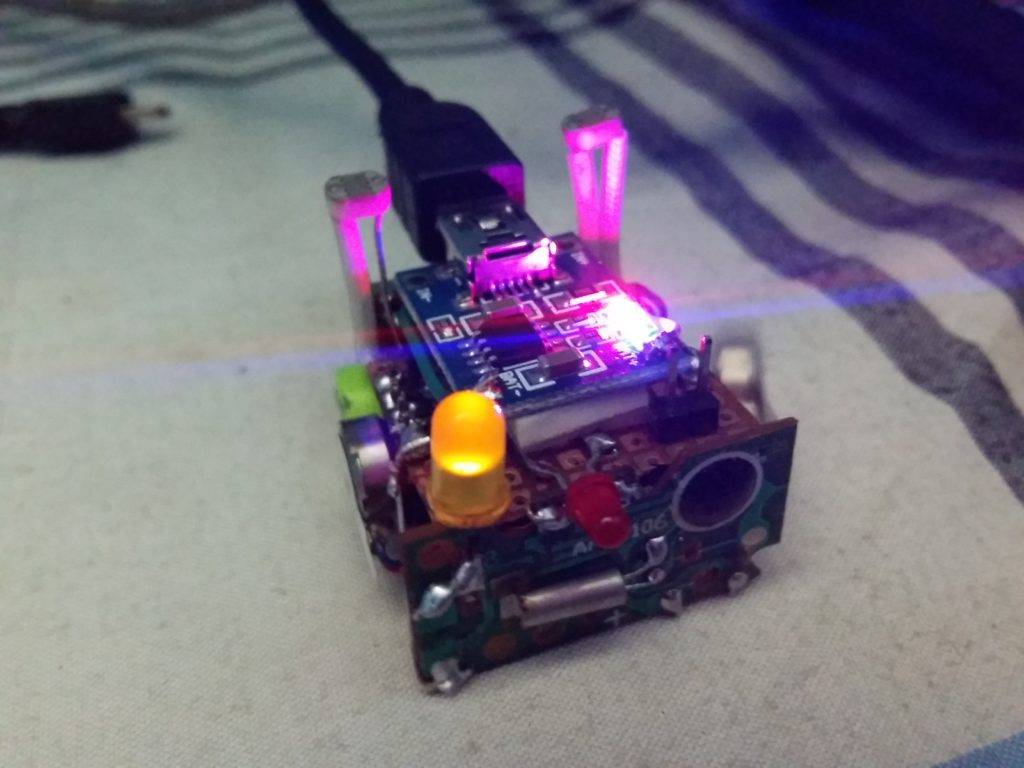
To date, only a few studies have been conducted on the use of microrobots in minimally invasive surgery. However, as methods of propulsion and control have improved, microrobots could find a wide range of potential applications throughout the human body.
Soft microrobots must move in undulating motions to generate thrust that propels the body forward. In order to create a flagellar drive, we must overcome two major hurdles.
First, the soft micro-robot has to react to an external stimulus.
Second, the external stimulus must be controlled to provide predicted propulsion and steering.
Engineering Microrobots
A magnetic field is commonly used to actuate and control soft microrobots. This chapter begins with a brief overview of classical electromagnetic theory.
We describe the magnetic field generated by magnetic material and electromagnetic coils and the magnetic force and torque exerted on the soft magnetic material of microrobots.
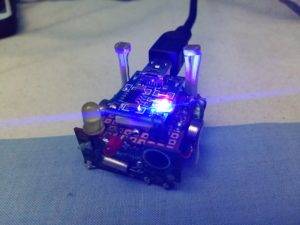
We will then address the soft microrobot boundary actuation problem by using an external magnetic field to generate passively propagating transverse waves along a filament.
Bug Like Micro Bots a Boost
MIT researchers have demonstrated tiny drones that can fly around with beetle-like agility and resilience, and could eventually accomplish those tasks.
The soft actuators that power these microrobots are very durable, but require much higher voltages than similarly sized rigid actuators. The featherweight robots cannot carry the necessary power electronics that would allow them to fly on their own.
Now, these researchers have developed a manufacturing technique that allows them to build soft actuators that operate at 75 percent lower voltage than current versions while carrying 80 percent more payload. These soft actuators are like artificial muscles that rapidly flap the robot’s wings.
This new manufacturing technique produces artificial muscles with fewer defects, dramatically increasing component life and increasing the robot’s performance and payload.
“This will open up many opportunities for us to switch to installing power electronics in the micro robots in the future. People tend to think that soft robots are not as powerful as rigid robots. We show that this robot, weighing less than a gram, flies the longest in hover with the smallest error.
MIT Performance of Flying Micro Robots
The take-home message is that soft robots can outperform rigid robots,” says Kevin Chen, assistant professor for D. Reid Weedon, Jr. ’41 in the Department of Electrical Engineering and Computer Science.
The director of the Laboratory for Soft- and Micro robotic in the Electronics Research Laboratory (RLE) and senior author of the article.
Chen’s co-authors include Zhijian Ren and Suhan Kim, co-lead authors and EECS PhD students; Xiang Ji, a research scientist in EECS; Weikun Zhu.
A chemical engineering graduate student; Farnaz Niroui, Assistant Professor at EECS; and Jing Kong, professor of EECS and principal investigator in RLE.
https //aka.ms/remoteconnect
The research was accepted for publication in Advanced Materials and was included in the journal’s Rising Stars series, which recognizes outstanding work by young microlab scientists.